Warehousing in the US is a large industry, employing 7.4 million people in 2020. The public storage and warehousing market in the US, meanwhile, is worth $30.9 billion as of 2022. That’s a lot of businesses handling a lot of orders—and they all need to keep up with increasing customer demand for speed, convenience, and personalization.
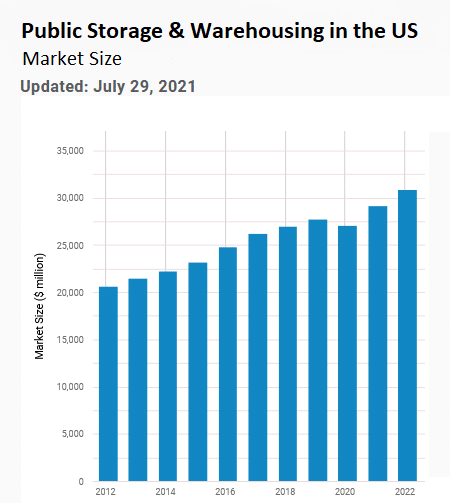
Source: ibisworld.com
What is warehouse shipping software?
Warehouse shipping software is basically a category of software that’s designed to automate and optimize the processes involved when goods leave your warehouse and make their journey to the end customer. It’s tightly connected to warehouse management, as they are two adjacent stages of the supply chain.
It’s possible to purchase standalone shipping software, but you have to make sure it will work seamlessly with your Warehouse Management Software and other systems. That’s why it’s usually more effective if your WMS is already part of an integrated solution with shipping capabilities built in, which makes it easier to manage all operations in one place.
Warehouse shipping software should integrate with all the major shipping carriers, and automatically select the best rates based on your pre-set rules. Automation means you don’t have to manually assign orders to warehouses, and you can track your orders all the way to delivery (and keep customers in the loop).
You should also be able to print custom shipping labels and documentation, edit shipment details, and generate invoices and bills of lading. Smart shipping software also means you can easily split orders, use dropshipping, and offer BOPIS (buy online, pick-up in store) as well as simple returns management.
To fully understand warehouse shipping software and choose the right one you first need to understand warehouse management software (WMS)…
What is a Warehouse Management System?
A Warehouse Management System, usually referred to as a WMS, is a software solution that helps businesses optimize their warehouse practices. It’s a set of tools that combine to streamline all the processes involved in warehousing, usually through automation.
A WMS is typically focused on the period when goods are in your warehouse or distribution center, which includes receiving, storage, picking, packing, and dispatching—as well as inventory tracking and labor management. However, it’s also connected to other parts of the supply chain, covering the movement of goods in and out of your facility.
The software provides assistance by managing tasks and syncing data in a centralized system, helping you optimize resource use, improve accuracy, and meet consumer demand. The aims are to save you time and money, ensure you have the right amount of stock, and avoid delivery delays.
Types of Warehouse Management Systems
There are several different types of WMS, and the one you choose will depend on the size and type of your organization. A Warehouse Management System might be part of ERP (Enterprise Resource Planning) or Supply Chain Management (SCM) software, or it might be a separate system.
There is increasing crossover between the models—some ERP vendors are adding warehouse management functionality, while dedicated WMS software now often includes supply chain visibility and other capabilities.
Standalone Warehouse Management Systems
Standalone WMS solutions, as the name suggests, are specialized products with warehouse management capability and nothing else. They offer basic WMS functionality such as automation for warehouse operations like picking, packing, and shipping, and inventory management features such as barcode scanning and slotting.
This software is available as on-premises systems or based in the cloud. In most cases, it can be combined with other software for supply chain logistics, such as ERP or transportation system management. However, you’ll have to ensure that the systems work together smoothly, and it won’t be as seamless as choosing an all-in-one platform like Brightpearl.
Standalone systems include HighJump, Fishbowl, and 3PL Warehouse Manager. There are also some free open-source versions but these probably won’t be robust enough to handle complex warehouse management.
Source: softwareadvice.com
Supply chain execution modules
Some WMS solutions are included as modules within a wider Supply Chain Management (SCM) suite. SCMs are specifically designed to streamline key supply chain processes like inventory control, sourcing of materials, product cycles, and risk management—as well as encouraging strong relationships with suppliers and shipping carriers through communication.
Large businesses that require a high degree of control over complex operations may choose to invest in Supply Chain Management systems. The warehousing features contained within an SCM are designed to operate smoothly as a critical link in the chain, and sync their data with the other modules.
SCMs can also be integrated with other business software such as payroll and ERP. Examples of this type of software include SAP SCM and Infor SCM.
Integrated ERP systems
Like SCM, ERP software may provide warehouse management as a module within a broader solution. An ERP is an integrated all-in-one system incorporating aspects such as supply chain planning, accounting, customer relationship management, and human resources.
ERPs like Oracle NetSuite and Microsoft Dynamics help you centralize your operations in a single interface. Specific WMS capabilities may include automated operations and inventory management, but you have to remember that warehouse management is not a core function of ERP solutions. You’re better off with a retail operating system like Brightpearl.
Cloud-based Warehouse Management Systems
Many businesses are moving to cloud-based warehouse management solutions, as they are far more accessible and flexible than traditional on-premises systems. All the tools and data are housed in the cloud instead of on physical hardware in your facility, which means there’s nothing for you to install or maintain.
Cloud-based systems such as Brightpearl are sold on a SaaS (Software as a Service) basis, where you lease the software from a vendor who retains overall responsibility—meaning lower total cost of ownership for your business. They are fast to deploy, easy to use, and highly scalable.
This type of software is especially useful for multi-location warehouse operations, as the system can be accessed from any device with an internet connection. Warehouse staff and managers, therefore, have all the information they need via handheld devices and tablets as they move around the floor and make updates.
What are the advantages of using a Warehouse Management System?
Warehouse management software has many benefits, from optimized processes and reduced labor costs to improved customer satisfaction and better security practices. If you’re not already convinced that this is an essential part of your business, keep reading as we look at some of the key advantages.
Better customer service
As well as making a profit, the main aim of your business is to keep your customers happy. Excellent warehouse management can help you do that. If you use the right WMS software, you’ll have increased visibility of your inventory and more control over the inbound and outbound movement of goods, which makes it easier to ensure your stock levels match real-time customer demand.
This means you can minimize the risk of stockouts, which are disappointing for customers—it’s frustrating when they see an item listed for sale on your website, only to learn that it’s actually unavailable. And if you do experience a stockout for a particular item, you can allow customers to place backorders because you know exactly when the item will arrive.
Efficient warehouse management also helps you avoid mispicks, mispacks, and delivery delays. It means you can confidently offer customers more complex options, such as expedited shipping, flexible order fulfillment (like BOPIS or dropshipping), and a simple returns process. Tracking orders enables you to send accurate confirmations, shipping updates, and invoices.
Plus, with an integrated system, you can also use data from your CRM to personalize customer service.
Optimized processes
In a study on the future of warehousing, 60% of organizations said that productivity and labor efficiency were the key challenges driving the adoption of automation technology. Warehouse Management Systems enable you to meet those challenges, not just through automation but through general efficiency.
Source: selecthub.com
A WMS helps you to streamline all your warehouse processes so that they are faster, smarter, and more accurate. For example, there’s no need for manual data entry because the system gathers data at every stage—so you automatically get fewer human errors. Auto-generated pick lists, packing slips, and shipping labels mean staff can process orders faster, and have them ready at the dock when the delivery truck comes to collect them.
WMS systems incorporate barcode and RFID (radio frequency identification) scanners to log and locate items quickly, which is a bonus for cycle counting and audits, as well as receiving and inspecting goods and ensuring they are stored correctly. Warehouse managers can easily adjust workflows according to demand.
ERP integration
As we mentioned already, it’s often possible to link your WMS solution with an ERP, or to buy an ERP with built-in warehouse management functionality. Having an integrated system in place has obvious advantages for efficiency, as all the tools work together smoothly and data from multiple systems is synced and centralized. This means you can analyze performance and identify ways to improve.
However, if you need more robust warehouse management capabilities than an ERP can provide, and if you want the seamless nature of an all-in-one solution rather than linking two separate pieces of software together, Brightpearl is a great alternative. The retail operating system has everything in one place already—not just an advanced WMS but also order management, fulfillment and shipping, supplier management, CRM, accounting, and business intelligence.
Cost-efficiency
Warehouse management systems help you to organize your workforce. You can ensure you have enough staff to meet demand at busy periods, but you won’t be paying people to stand around when it’s quiet. Plus, you can significantly reduce labor costs with automation, which is especially effective for highly labor-intensive tasks such as picking.
Source: selecthub.com
By giving employees smart tools and allocating them to the right places at the right times, you’ll boost productivity, saving you time and money. With automated documentation and data entry, accuracy is also improved, which means you won’t have to send replacement items to customers after a mistake, or compensate them for a delayed delivery.
When you’re confident that your system is operating smoothly, you can offer expedited delivery without losing profits or operate a just-in-time inventory model for further cost savings. Meanwhile, as discussed earlier, a cloud-based tool is far cheaper than an on-premises system.
ROI
Although you can make significant cost savings with a cloud-based solution, best-in-breed WMS or integrated software still represents a large investment. But if you make sure to choose a smart system that helps you meet your challenges, you’ll end up with an impressive ROI. Do your research and balance the overall cost against the number of features.
The ability to process orders faster (and more accurately) will help you satisfy customers, thus boosting sales and increasing profits. If your WMS has a robust analytics feature, you’ll be able to directly link ROI to increased efficiencies in warehouse operations like storage and packing. Don’t forget that evidence of ROI can be found even in non-quantifiable areas like positive customer sentiment.
Enhanced safety and security
As well as making your warehouse processes faster, good management will also help you make them safer to protect your workforce. In the USA in 2020, there were 206,000 non-fatal workplace injuries in the warehousing and transportation sector. Apart from being a responsible employer, you want to avoid employees having time off through injury or suing you for dangerous working practices.
An advanced WMS can highlight potential problems, and help you adjust workflows when necessary. For example, if goods are getting damaged, is it because staff aren’t trained to handle them? If your warehouse deals with dangerous items, everyone needs to be reminded of the special protocols for storage, handling, and shipping.
Warehouse management also includes security. Full inventory visibility means you can check for any theft of goods, and put safeguards in place for especially valuable shipments. The best warehouse management software will have advanced security settings to protect your company data and that of your customers.
How does a Warehouse Management System work?
Inventory management
Inventory control is a critical part of warehouse management. For true efficiency, you need to know the location and status of every item of stock at all times—not only when it’s in your warehouse, but also when it’s on order from suppliers, being transferred between locations, on shelves in a physical store, being delivered to the customer, or going through the returns process.
WMS solutions often incorporate technology like barcode scanners, which are used to log items as they arrive and also to track their journey through the warehouse. You might also have an audio alert system to help pickers find the correct items in a large warehouse. Both tools are helpful for inventory counts, as they update the central system automatically whenever an item is moved.
You can also keep an eye out for any damage, spoilage, or theft, and make accurate demand forecasts to ensure you replenish stock at the optimum time. The system will let you know when and what items you should order, and which supplier is most cost-effective for each order. Plus, you’ll know your exact stock levels when you respond to customer inquiries.
Source: techtarget.com
Work execution
Warehouse management includes receiving, inspection, sorting, put-away, picking, packing, and dispatch. If your business is handling large shipments or complex orders, it’s even more important that these operations are streamlined—and customized to suit your business needs.
Your WMS software will help you create suitable workflows for all your warehouse processes, many involving automation for maximum efficiency. You can plan work activities by task and area, allocate work assignments, and make sure everything is stored correctly, handled safely, and processed quickly with the correct documentation. And you can organize cycle counts without disrupting day-to-day operations.
A WMS also enables you to be agile and flexible, so that you can ramp things up in busy periods. You might want to switch between different types of picking, such as zone, wave, batch, cluster, and kitting. Or you could locate certain items closer to the shipping dock for ease of movement.
Reporting and analytics
Advanced analytics are also crucial for good warehouse management. You need the ability to monitor and evaluate individual employee performance, the overall performance of your warehouse(s), and how they fit into your business goals and affect the wider supply chain.
Typically, a WMS will display these metrics on a central dashboard, and generate simple or detailed reports. You’ll be able to spot problems before they happen, identify ways to improve, and offer more training to staff where necessary. Plus, you can monitor customer feedback to see changing behaviors and preferences.
Analytics are also used for demand forecasting—you can use historical data to identify peak times, ensure adequate staffing levels, and set reorder points. Replenishment reports show what you need to order, while product performance analytics help you decide which items are not selling well. You might also use data in price negotiations with carriers and suppliers.
Shipping
Although it doesn’t necessarily handle the shipping itself, a Warehouse Management System helps to ensure that customer orders are made ready for shipping as quickly and accurately as possible. This means you can offer a variety of shipping options, and easily handle dropshipping, multi-location fulfillment, or FBA. By optimizing the in-warehouse processes, you’re doing your part in making sure that deliveries arrive on time.
This involves pulling in details from your order management system to create accurate pick lists, packing slips, and auto-printed shipping labels. Of course, it helps if you’re using an all-in-one platform like Brightpearl, which also generates customs forms for international shipments, and uses automation to ensure the right contents (delivery notes, invoices, or even free gifts) are included in the right parcels.
The best Warehouse Management Systems will also enable you to liaise with carriers and choose the right method and optimum route for each delivery, as well as making full use of capacity on delivery vehicles. You might also want to set up a cross-docking station, and link your WMS with a yard management system.
How does shipping through a Warehouse Management System work?
As we’ve explained, warehouse management systems are largely focused on what happens when goods are in your warehouse or distribution center. But that’s not to say that they don’t have anything to do with shipping. It’s just that some WMS solutions have more advanced shipping capabilities than others.
It’s important to decide exactly what you need, which will depend on the size and complexity of your operations. For example, if you’re a small business that only processes a handful of local orders per day, you’ll only need one small vehicle to deliver them. But at enterprise level, you’ll need to coordinate with multiple trucks coming in and out at all times of the day.
The main thing to remember is that effective shipping is directly linked to the efficiency of your internal warehouse workflows, including inventory control, picking, and packing. If these processes don’t run smoothly, you’re going to end up with missed deliveries and unhappy customers.
Source: bigrentz.com
How to choose the best warehouse shipping software
Every warehouse is different, so it’s important to consider your specific requirements and challenges before making a final decision on warehouse shipping software. If you’re a large business operating multiple warehouse locations and selling products on multiple channels, your chosen solution will need to be able to handle that level of complexity.
You need to do plenty of research (and sign up for some free trials) in order to figure out which features are necessary and which are just nice to have. Obviously, your budget will be a major factor, too! And it’s important to pick a system that offers general ease of use.
Source: ascendixtech.com
Features to consider for your warehouse shipping software
Easy integration with current systems
If you’re operating a standalone WMS with shipping functions, you’ll need to connect it to separate systems for order management, SCM, yard and transportation management, or an ERP. Even if you go for an integrated tool, you’ll still want to link it to your other business systems such as accounting and CRM. How difficult or time-consuming will it be to achieve this?
Look for a system that makes it easy to integrate various systems and sync the data between them for a complete overview of your operations. Brightpearl, for example, includes robust shipping and fulfillment capabilities, but it also integrates seamlessly with shipping carriers, third-party logistics (3PL) firms, e-commerce platforms, marketing software, and more.
Cost
Everyone talks about finding “value for money”, but this means different things to different businesses. There’s no point in splashing the cash on a system with features you don’t actually need and won’t get full use from, but you also shouldn’t be tempted to skimp and opt for the cheapest solution. Ultimately, it has to be right for you, and scalable as you grow.
Check that the vendor offers transparent pricing and makes billing easy to understand. Cloud-based systems are more affordable because you just pay a monthly subscription and upgrade if you need to, which makes the cost predictable and reduces the total cost of ownership.
Remember to factor in the cost of mobile devices like tablets and barcode scanners—but you’ll soon make savings from the increased efficiency they bring. In fact, with Brightpearl, automation can reduce labor costs by 50%.
Source: zebra.com
Time it will take to implement
If you go for cloud-based software (which we’d highly recommend), there isn’t anything to install, so the system can be deployed a lot faster than an on-premises solution. Most warehouse management shipping solutions are designed to be easy to learn, which means all employees can be brought up to speed quickly and start being productive from the get-go.
When you choose an out-of-the-box solution, it’ll generally be faster and easier to set up compared to a fully customized system, so make sure you know what you’re getting and how long any adjustments might take. It’s important for scalability that you can make certain adaptations yourself, such as adding extra users for busy periods.
Warehouse shipping software capabilities
It goes without saying that your chosen software needs to have excellent shipping capabilities, no matter the size or type of your business. But the more packages you ship per day or per month and the more complex the fulfillment logistics, the more robust the software needs to be. The last thing you want is for the system to crash because it can’t cope with increased order volume.
That’s another reason why it makes sense to choose a highly scalable solution, so you know that it’s ready to handle those higher volumes and greater order complexity when your business gets to the next stage of growth. For example, Brightpearl is specifically designed for retail, which means you have all the required features but can also adjust your tech stack to meet changing conditions.
Maintenance
Maintenance is something you don’t have to worry about too much with a cloud-based system, because it’s all taken care of by your software vendor—saving you money and time. Updates and upgrades should arrive automatically (without disrupting your activities), so that all users are always accessing the latest version of the system for maximum productivity.
If you do want to make any adjustments, you can usually manage this yourself without calling the IT department. However, it’s worth checking the vendor’s own maintenance practices and uptime guarantees, as downtime can prove costly. Consider their security protocols, too, as you need to be able to reassure customers that their information is fully protected.
Source: prometheusgroup.com
What to consider when choosing warehouse shipping software based on your needs
Warehouse size
If you have a large warehouse or a network of distribution centers, your processes will likely be more complex than those of smaller businesses. You’ll be dealing with a large volume of goods, multiple employees, and a high number of dispatches and deliveries.
That means you need a system that helps you optimize space and layout, not just for improved productivity, but also for safety. In a big warehouse with multiple product lines, proper organization is essential to ensure pickers can always locate items quickly and get them to the packing and dispatch areas. As well as the physical size of the warehouse, consider the amount of data you have to keep track of.
Output volume
Another factor to consider is the number of shipments you’re putting out each day, week, or month. As we’ve mentioned, your warehouse shipping software must be able to cope with high order volumes and seasonal fluctuations. You may also need a yard management system to coordinate the efficient movement of trucks, trailers, and pallets.
Warehouse shipping software saves you money by choosing the most cost-effective carriers to use based on criteria like weight and location. It can also help you make the best use of space in trucks and containers, by logging the weight and dimensions of orders and arranging to share LTL (less than truckload) shipments with other local businesses.
Warehouse locations
Operating a number of warehouses in different strategic locations is ideal for expanding your storage capacity and reducing delivery costs by being nearer to your customers—but it’s an extra logistical challenge.
Advanced warehousing and shipping software is essential for orchestrating goods, processes, and labor across locations, as it gives you full visibility and ensures the whole system is updated in real time. Even if you only have one warehouse at the moment, it’s worth thinking about your future plans and opting for a scalable solution.
Shipping contents
If you have a wide range of product lines, you’ll need great organization to make sure the right items are picked from the shelves, packed in the most suitable packaging, and carried via the appropriate transport.
You’ll need to put separate protocols in place for specialized contents. For example, making sure that fresh produce is assigned to refrigerated trucks or containers, or that dangerous goods are properly labeled. Shipping speeds also need to be adjusted accordingly, and delivery windows arranged so that customers are able to sign for high-value items.
An advanced software solution can also ensure that you maintain compliance with any regulations, and have the right documentation for international shipments. It would be a disaster if your shipment was denied entry to an overseas port!
Weight of shipping items
The weight of your goods is also an important consideration. You’ll want to keep the packaging weight as low as possible while ensuring the items are properly protected in transit, so make sure the packing team are given the right materials and instructions to make this possible.
Obviously, you’d need to send very heavy items via rail or sea, while air transport can help you keep your next-day shipping promise. Costs can rise quickly if you use an inefficient shipping method, and remember that some carriers will have weight limits. It’s easy to do a cost comparison on their websites.
Instead of manually choosing and assigning a carrier for each order based on weight, you can let the software do it for you. Brightpearl integrates with all major carriers so you have plenty of choice, and it helps you figure out how to maximize transport capacity.
Brightpearl for your warehouse shipping software
One of the many advantages of using Brightpearl is that it’s designed for e-commerce businesses by retail experts, which means you get a set of retail-focused features that you’ll actually use—plus excellent implementation, training, and support.
It’s cloud-based SaaS, with all the associated benefits of cost-effectiveness, fast deployment, and flexibility. The system is hyper-scalable and extends to suit your changing needs with an adjustable tech stack of built-in tools and native connections.
Benefits of using Brightpearl’s warehouse shipping software
Brightpearl’s warehouse shipping capabilities are robust enough to handle high order volumes and advanced enough to support complex logistics. Because it’s a comprehensive retail operating system with all your tools in one place, the shipping element is fully integrated and synced with all other aspects of warehousing and supply chain management.
That means you have full visibility of your operations, ensuring complete inventory accuracy. All your sales channels, warehouses, customers, and suppliers are interconnected in one central hub and data is synced in real-time whenever an order is picked, packed, and shipped.
Automation is a major benefit of Brightpearl, optimizing your workflows for maximum efficiency and cutting shipping time by 92% (which also saves you money). For example, if an item is out of stock in your physical store, you can use the POS to view availability, fulfill orders from another location, or automatically mark unavailable items as back orders.
The raft of real-time data provides opportunities for in-depth analytics and demand forecasting, with the added bonus of replenishment alerts and reports, and product performance analysis. You can also stay in control of your finances by automatically generating purchase orders and invoices—use the built-in retail accounting feature or the integration with QuickBooks or Xero.
Brightpearl integrates with all the major shipping carriers including Shipstation, Shiptheory, and Parcelhub, and lets you easily manage them all in one place. This allows you to use a multi-carrier strategy, which is more effective for e-commerce fulfillment and shipping. Brightpearl is also a certified partner of Shopify and Shopify Plus, BigCommerce, and other e-commerce platforms.
Key features of Brightpearl’s warehouse shipping software
With direct plug and play shipping integrations, including native connectors to Amazon FBA and 3PL providers, you can offer plenty of shipping options and ensure you get orders out of the door—and to the customer’s door—quicker than ever.
The Automation Engine will select the most suitable carrier for each order based on criteria you put in place, such as the price, weight, or quantity of products. This can reduce delivery shipment costs, as well as the time between customers ordering goods and receiving them.
Another way to reduce shipping costs is to maximize container loading, and Brightpearl’s Inventory Planner can help you do just that. It enables you to add CBM (cubic meters) or weight for each item and pull the details into your purchase orders, to ensure you fill every square inch of your shipping containers efficiently.
You can also set up rules for automating other shipping and fulfillment tasks, such as dropshipping items for certain customers, channels, or products. Batch shipments together based on your preferred criteria, and create the most efficient pick routes through the warehouse to get orders out faster.
Brightpearl can be programmed to automatically use older inventory first, and choose the best inventory location to fulfill each order so that you don’t need to transfer products between warehouses before shipping. You can also automate order splitting when certain items are out of stock—the system will automatically fulfill backorders when stocks are replenished.
The Automation Engine also covers shipping labels, packing slips, and customs documents for international orders. Pickers and packers always receive accurate information, while barcode scanners and audio alerts help them locate the correct items. You can create channel-specific templates for packing notes, and even set the system to include a gift in VIP orders (using the built-in CRM to segment your customers).
Once an order is shipped, you can track it along its journey by syncing data with your carriers, and provide customers with regular updates. Returns management is also made simple—when customers send items back to you, Brightpearl automatically initiates the sales credit process as soon as the items are received in the warehouse.
Brightpearl’s WMS feature has a separate login and interface for your warehouse management team, which ensures they have all the information, workflows, and functionality they require. Which makes the warehouse shipping process a whole lot easier!
Final Thoughts
Warehouse management is a crucial part of the supply chain. Whether your WMS is a standalone solution or integrated with an SCM or ERP system, it has to work seamlessly with the other components that make it possible to fulfill and ship orders quickly and accurately.
Your warehouse shipping software also needs to integrate with your current tech stack, and be scalable enough to adapt to an expanding business and changing market conditions. If your workflows and processes are disrupted by glitchy connections that struggle with high volumes, you’re going to face delays and customer complaints.
77% of decision makers in the warehousing industry agree that they need to modernize their warehouse operations to remain competitive, but admit they are slow to implement new mobile devices and technology. Make sure you stay ahead of the game by choosing an advanced solution for warehouse shipping—such as Brightpearl.
As a retail operating system, Brightpearl provides far more functionality than either a standalone WMS or an integrated ERP. It’s flexible, scalable, easy to use, and the automated tools can cut your labor costs in half. For more information, check out the website and book a demo.